婴幼儿配方乳粉生产企业蜡样芽胞杆菌风险防控指南(市监特食发〔2025〕16 号)
发布时间:2025-04-11 浏览次数:54 分享:
附件1
婴幼儿配方乳粉生产企业蜡样芽胞杆菌风险防控指南
一、蜡样芽胞杆菌的基本特性
蜡样芽胞杆菌是常见的食源性致病菌,革兰氏阳性,需氧或兼性厌氧,菌体细胞杆状,产芽孢,在自然界中分布广泛,存在于土壤、空气、水和尘埃中。蜡样芽胞杆菌部分菌株能产生肠毒素,通常包括致呕吐型毒素和致腹泻型毒素两类,感染症状通常表现为恶心、呕吐和腹泻等胃肠道感染症状。我国一直将其视为婴儿配方乳粉风险防控的重要指标。
蜡样芽胞杆菌营养体最低生长温度约为4—5℃,最高生长温度约为48—50℃,常温下6h左右即可进入对数生长期,允许生长的 pH 值范围为 4.9—9.3,生长的最小水分活度为 0.912— 0. 950;产生的芽孢对热、冷冻、干燥和紫外线辐射等条件有很强的耐受性,且一旦条件理想芽孢就会萌发转化为营养体。从食品微生物学角度来看,蜡样芽胞杆菌具有耐热性强、不易杀灭的特点。
二、生产过程中蜡样芽胞杆菌的危害识别与风险分析
(一)湿法工艺
基于危害分析与关键控制点(HACCP)原理,结合婴幼儿配方乳粉湿法工艺生产过程主要环节的危害识别与风险分析结果(见附录1),风险较为显著、对风险控制有重要作用的工艺环节主要包括:
1.原料控制
原料中的蜡样芽胞杆菌水平对于后续生产过程中的各项控制措施及终产品的污染风险具有决定性影响,尤其对于使用生乳为原料的工艺过程,生乳中蜡样芽胞杆菌风险的暴露性高、可控性低,且在运输过程中有增殖的风险,是生产过程中蜡样芽胞杆菌污染的最主要来源。
2.杀菌
杀菌通常应作为蜡样芽胞杆菌危害的关键控制环节。
巴氏杀菌能够杀灭蜡样芽胞杆菌的营养体,但芽孢能在巴氏杀菌后残留下来,甚至一定数量的芽孢可能经热处理诱发萌发。
婴幼儿配方乳粉生产企业中常用的蒸汽直接喷射杀菌(DSI)工艺通常情况下能够有效杀灭蜡样芽胞杆菌及芽孢,但在杀菌参数偏离、杀菌前产品微生物污染水平过高等情况下,依然有蜡样芽胞杆菌残存的可能性。
3.中间贮存
在包括生乳贮存、巴氏奶贮存、配料贮存、浓奶贮存在内的多个中间贮存环节,贮存温度、时间对于蜡样芽胞杆菌风险控制至关重要。应注意4℃左右的低温环境,仅能对蜡样芽胞杆菌进入对数增殖期起到延缓作用,并不能有效抑制其生长繁殖。任何中间贮存超出限定温度、时间的情形,都可能导致蜡样芽胞杆菌数量增长超出可控范围。
4.清洁与消毒
蜡样芽胞杆菌在食品加工设备内表面有较强的黏附性,结合其不易杀灭的特点,容易在生产线上污垢积存的点位孳生。因此,清洁与消毒是清除生产线中残存蜡样芽胞杆菌的重要手段;相反,清洁或消毒不彻底则是造成婴幼儿配方乳粉生产过程中蜡样芽胞杆菌污染的重要原因。
5.蒸发浓缩
在长时间连续生产的情形下,蒸发浓缩环节的蜡样芽胞杆菌风险会显著升高,浓奶在蒸发浓缩器内表面积累形成奶垢为蜡样芽胞杆菌孳生提供了条件,当达到一定水平后,由于蒸发浓缩处于杀菌工序后端,终产品中的蜡样芽胞杆菌水平将难以控制。
车间环境、生产人员卫生状况、包装材料、设备设施、生产操作可能出现的交叉污染等都是造成蜡样芽胞杆菌污染的潜在风险,但在严格执行良好生产规范的基础上,一般不需要采取额外控制措施。
(二)干法工艺
基于危害分析与关键控制点(HACCP)原理,结合婴幼儿配方乳粉干法工艺生产过程主要环节的危害识别与风险分析结果(见附录2),风险较为显著、对风险控制有重要作用的工艺环节主要包括:直接进入干混合工序的原料、食品添加剂可将微生物直接带入产品,是干法工艺蜡样芽胞杆菌污染风险的主要来源,尤其是以含乳原料为载体的干混原料(如以乳清粉为载体的二十二碳六烯酸、二十碳四烯酸等)。车间环境、生产人员卫生状况、包装材料、设备设施、生产操作可能出现的交叉污染等都是造成蜡样芽胞杆菌污染的潜在风险,但在严格执行良好生产规范的基础上,一般不需要采取额外控制措施。
三、蜡样芽胞杆菌的控制措施
生产企业在确保严格执行良好生产规范的基础上,可依据工艺类型特点,对以下要素加强管理,必要时建立针对性风险监控计划或风险防控措施:
(一)湿法工艺
1. 生乳的收集与储运
(1)奶源基地管理
严格控制自建或自控奶源基地的牧场环境、牲畜、挤奶设备及操作过程的卫生状况,注意保持圈舍卧床干燥清洁,及时清理粪便、防疫消毒,做好挤奶过程相关人员、牲畜、挤奶设备的清洁消毒。可根据自身情况,配备覆盖牧场挤奶器、板式换热器、奶罐等设备设施的就地清洗(CIP)系统。
加强牲畜病疫管理,做好分群管理及病畜隔离工作,可通过加强监测和及时治疗等手段降低病疫的传播及其对相应微生物水平的影响。
可根据自身情况开展对自建自控奶源基地(环境、牲畜、设备设施、生乳等)的微生物监控。
(2)生乳储运
应严格执行“生乳在挤奶后2h内应降温至0—4℃”的要求,运输过程温度控制在0—6℃。
宜制定牧场生乳储存设备、生乳运输车辆清洗消毒规程(宜配备覆盖生乳运输车辆、收奶软管等的CIP系统),严格执行并定期进行效果验证。
2. 原料验收与监控
对于使用生乳为原料的生产企业,宜结合自身情况建立生乳中蜡样芽胞杆菌风险监控计划,制定监控限值,明确检验结果超限后的处置程序及加严控制的相关措施。注意控制生乳原料取样到加工使用的时间间隔,确保检验结果能够反映加工使用前的蜡样芽胞杆菌水平。
对用于婴幼儿配方乳粉生产的其他原辅料,宜基于风险分析制定蜡样芽胞杆菌验收标准或建立风险监控计划。
3.中间贮存
应严格控制生乳贮存、巴氏奶贮存、配料贮存、浓奶贮存等中间贮存环节的贮存条件与贮存时间。必要时建立相应的风险监控计划,定期监控中间贮存产品的蜡样芽胞杆菌水平。
4.生产过程控制
严格执行各杀菌工序工艺参数的控制要求,如果偏离限值应采取恰当的纠偏措施。
宜制定配料、蒸发浓缩连续生产控制要求,根据连续生产过程中微生物增殖情况的评估结果,针对连续生产时间、是否执行中间清洗操作、中间清洗操作标准程序等做出明确规定,严格执行并定期验证。
可结合自身情况,采取在线取样等方式开展监控。
5.清洁与消毒
应严格执行清洁消毒技术要求和管理流程,定期进行效果验证。
可定期采用过氧乙酸类的消毒剂对设备内表面进行消毒。
可对CIP 难以清洗的点位(如蝶阀、集气瓶、双联过滤器、小料斗、部分垫圈缝隙、卫生设计缺陷导致的污垢点等)进行识别,在CIP 结束后进行手动拆洗;对于板式换热器、杀菌器、分离机、净乳机等容易积垢的设备制定检查计划,定期手动拆卸进行检查并彻底清洗消毒。
6.成品检验
可将蜡样芽胞杆菌纳入婴儿配方乳粉成品检验指标。
(二)干法工艺
对于直接进入干混合工序的原料、食品添加剂(特别是含乳原料为载体的干混原料),宜制定蜡样芽胞杆菌验收标准或建立风险监控计划。
四、蜡样芽胞杆菌污染的调查
宜制定调查方案,以便在发现蜡样芽胞杆菌污染时能够及时有效开展调查、评估风险。调查方案可参考附录3中列出的调查方式和要素,采用分段调查方式缩小调查范围,通过取样检验和分析调查并用的方式,锁定污染点、查明污染原因,以便清除污染并消除造成污染的风险。
五、生产线上蜡样芽胞杆菌污染的清除
在常用的消毒剂中,过氧乙酸类消毒剂对蜡样芽胞杆菌清除作用最好,杀灭效果随杀菌剂浓度和杀灭时间的增大而增强。理论上100mg/L 过氧乙酸溶液作用30min或 1000mg/L 过氧乙酸溶液作用15min 可有效杀灭生产线上残留的蜡样芽胞杆菌;标准CIP 程序配合 3g/L 过氧乙酸溶液 25℃冲洗 10min可以有效清除蜡样芽胞杆菌污染。企业在实际操作过程中宜根据消毒剂使用说明中的浓度要求,经验证后使用。
附录3
附件2
婴幼儿配方乳粉生产企业克罗诺杆菌风险防控指南
一、克罗诺杆菌的基本特性
克罗诺杆菌隶属于肠杆菌科,革兰氏阴性,兼性厌氧,无芽孢,在自然界中分布广泛,存在于土壤、空气、水和尘埃中。克罗诺杆菌是一种食源性条件致病菌,对于0—6月龄婴儿(特别是免疫功能受损的婴儿)能够产生较大威胁,感染后易引发精神萎靡、拒乳、黄疸加重等症状,严重者可引起坏死性小肠结肠炎、败血症、脑膜炎等,《食品安全国家标准 预包装食品中致病菌限量》(GB29921—2021)规定在 0—6 月龄婴儿配方食品中不得检出。
克罗诺杆菌能够在8—47°C的温度范围条件下生长,最适生长温度为35—40°C,但对 60℃以上的高温非常敏感,耐热性差;适宜生长的 pH值范围为 5—8,具有耐酸性强、不耐碱的特点;具有较强的抵抗干燥或高渗透压的能力,可长时间生存在水活度较低的环境中。
二、生产过程中克罗诺杆菌的危害识别与风险分析
基于危害分析与关键控制点(HACCP)原理,婴幼儿配方乳粉湿法工艺、干法工艺生产过程主要环节的危害识别与风险分析结果分别见附录1、附录2。
由于克罗诺杆菌耐热性差,通常巴氏杀菌、蒸汽直接喷射杀菌(DSI)及热处理过程可以将其有效杀灭,因此,湿法工艺中喷雾干燥/流化床二次干燥前段加工过程中的风险相对可控。
湿法工艺中喷雾干燥/流化床二次干燥后段、干法工艺全过程的生产操作、人员、设备、环境等要素交叉污染带入是克罗诺杆菌风险的主要来源,例如:
清洁作业区环境潮湿、粉尘积累导致克罗诺杆菌孳生;
人员、原辅料、包装材料、废物、工器具等由清洁度要求低区域进入清洁度要求高区域引入污染;
通风系统(包括干燥塔、流化床进风系统)送风引入污染;
用于食品生产、清洁食品接触面和设备的压缩空气或其他气体引入污染等。
干法工艺中直接进入干混合工序的原料、食品添加剂污染带入也是克罗诺杆菌风险的重要来源。
三、克罗诺杆菌的控制措施
克罗诺杆菌污染具有偶发性、“针点性”的特点,生产企业应在确保严格执行良好生产规范的基础上综合控制,重点注意对以下要素加强管理,必要时建立针对性的风险监控计划或风险防控措施:
(一)保持清洁作业区干燥
做好并保持不同洁净级别作业区之间、湿区域与干燥区域之间的有效物理隔离(宜包括夹层与屋顶间的区域);清洁作业区内,生产时应禁止用水;严格控制清洁作业区可能出现的各种水分来源,包括外部渗漏、设备设施渗漏/凝结、湿式清洁水分残留等,在清洁作业区内采用湿式清洁的,宜针对设备和环境恢复干燥制定操作规程并严格执行。
(二)环境监控
严格执行良好生产规范中对于清洁作业区、准清洁作业区动态控制、微生物监控的相关要求,监控项目检测方法有明确标准依据的,应严格按照标准进行取样、检测。
宜采取措施确保动态控制、微生物监控的有效性,例如:
严格执行测试规则、测试状态要求,测试状态为动态的,应在正常生产状态进行,避免清洁消毒等因素对测试结果的影响;
制定方案对取样、检测使用的耗材(如棉签、海绵等)、试剂盒等进行验收,可将肠杆菌科回收率作为验收指标;
制定涂抹取样操作规程并严格执行(涂抹取样方法可参考附录3),取样后尽快送实验室进行检测;
对目标微生物克罗诺杆菌和环境卫生水平指示菌肠杆菌科进行同步监测,指示菌监测不能取代目标菌监测;
长时间监测结果持续为阴性/无异常的情况下,特别是进出清洁作业区人员数量增多、车间改造等可能影响环境维持的因素出现后依然无异常的,注意考虑对监测有效性进行评估。
宜根据受污染风险(切实结合产品/原料暴露情况、物料流转路线、人流路线及流量、设备设施特点、环境要素等进行评估)、历史监测数据趋势分析、生产周期、厂房面积等要素动态调整取样区域、取样频率。建议取样区域重点覆盖以下点位:
产品直接接触面,如罐体内表面、传输产品的管道、筛网、软连接、呼吸帽、过滤器、采样器、与原料/产品直接接触的工具等;
封闭型生产设备内外部联通处,如设备的开口、舱门、进气口等;
紧邻产品和/或生产设备外表面及生产操作过程接触面,如设备外壳/框架、设备外表面间隙和缝隙、工作站、控制面板、秤、推车等;
人流频繁经过或接触点,如更衣室(特别关注区域间隔的门把手)、梯子、升降机、可拆卸台阶、叉车等;
粉尘容易聚积、残留的点位,如粉尘收集设备设施(负压称量罩、粉尘收集器等)、清洁工具及存放处等。
(三)人员卫生
严格落实良好生产规范中的食品加工人员卫生要求。特别注意清洁度要求低区域进入清洁度要求高区域人员净化流程的执行。做好工作服管理,严格执行工作服清洗消毒要求,宜特别关注工作鞋底可能造成的交叉污染。宜对进入清洁作业区人员的数量、出入频次进行控制。
(四)直接进入干混合工序的原辅料及包装材料控制
严格执行对于直接进入干混合工序的原料、食品添加剂及包装材料的验收程序,确保微生物指标符合产品标准要求。宜建立机制加强原辅料、包装材料供应链的生物危害评估与管理。
(五)压缩空气或其他气体监控
宜建立监控计划定期对用于食品生产、清洁食品接触面和设备的压缩空气或其他气体进行取样并进行微生物指标监控。
(六)清洁与消毒
应严格执行包括设备、工器具、环境等在内的各项清洁消毒技术要求和管理流程,定期进行效果验证。在清洗剂、消毒剂的选择方面,克罗诺杆菌对硝酸溶液、次氯酸等酸性清洗剂、消毒剂具有耐受性,而乙醇消毒剂、过氧化物类消毒剂、氢氧化钠溶液、漂白粉(次氯酸钙)则对克罗诺杆菌具有较好的杀灭效果。
宜加强对干燥塔清洁程序的监控(如清洗参数、烘塔温度等)和清洁效果的检查(如手动清洗点、清洗死角等,注意对塔内焊缝开裂等隐患的检查与发现)。
(七)停产复产管理
宜加强对企业停产复产(包括主动与被动)情形的管理。对于长期停产后复产、间歇性生产、停产复产较为频繁的生产企业,宜制定停产复产相关的管理制度或操作程序并严格执行。
对于停产期间生产环境条件发生重大变化的(如生产车间构造布局调整、生产车间结构破损维修、设备布局调整、空气净化系统维修或改造等情形),宜制定风险评估方案,对微生物污染等风险情况进行全面评估、处置、验证后方可复产。
四、克罗诺杆菌风险的调查与纠偏
宜制定克罗诺杆菌风险异常调查与纠偏方案(可参考附录4)。当风险监控出现异常时,如成品或过程样品检出克罗诺杆菌、环境监控发现异常(肠杆菌、克罗诺杆菌)或其他因素(如压缩空气等)监控出现异常等,应及时启动调查与纠偏程序。同时,对异常结果当天及前后数天内的成品增加抽样检验密度,加强风险防控。
附录3
表面微生物监控涂抹取样方法
使用浸有无菌采样液的拭子/涂抹海绵,在一定区域内(如5×5cm210×10cm2、25×25cm2 等,根据实际情况选择能够显示出环境微生物状况的最小面积作为采样面积)分别进行水平方向、垂直方向、对角线方向的反复涂抹采样(见下图,涂抹次数应与取样面积匹配,确保充分覆盖全部取样区域),并随之转动拭子。对于不规则表面应尽量涂抹交叉位置。采样时间30s左右。完成采样后,无菌剪去/折去手接触涂抹棒部分,将涂抹后的拭子/涂抹海绵放入装有采样液的试管/采样袋中保存或直接送检。
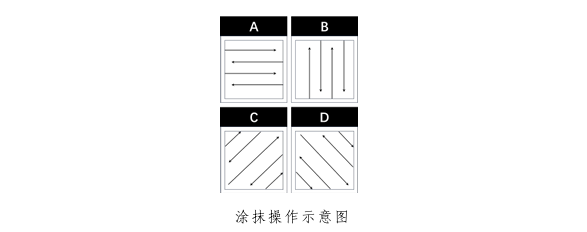
采样液可根据不同监测目标并充分考虑对工厂实际使用消毒剂组分的中和作用进行选择(如磷酸盐缓冲液、无菌生理盐水、无菌缓冲蛋白胨水、其他中和缓冲液等),以保证监测目标微生物活性,避免消毒剂残留可能产生的抑制或杀灭作用,使检测结果更准确。
采样应符合无菌操作的要求,一件采样器具只能盛装一个样品,防止交叉污染
采样后,对所采区域进行清洁和消毒,以避免采样过程在采样点位表面处残留营养物质。
使用商业化表面微生物采样产品的,应注意参照产品说明书进行操作
来源:网络转载,转载于“国家市场监督管理总局”